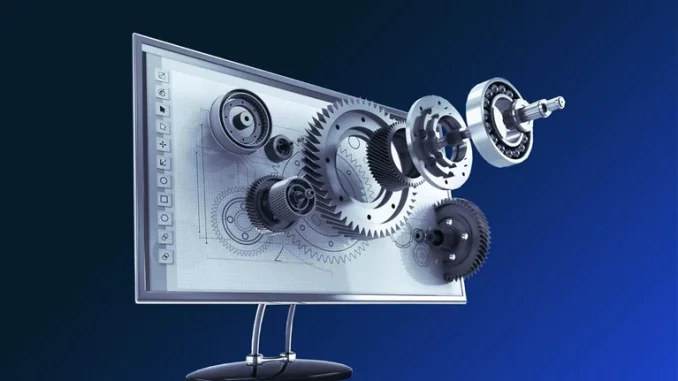
In today’s fast-moving manufacturing industries there is one connection between new technologies and traditional industrial society–they all serve the goal to upgrade industry. Digital Twin which can replicate physical assets, processes and systems (like the human body resembles itself at different ages) is bound to be a big winner in this era: The current explosion in demand for precision, efficiency and sustainability is driving companies towards digital twins as the primary means of improving industrial production and operations technologies. What Is a Digital Twin?
A digital twin is not simply some static digital model; it is a real-time, ever-changing representation that interacts with its physical counterpart. By collecting data from sensors embedded in the physical assets that a digital twin is modeling, it can accurately recreate the conditions, behavior and performance of these physical assets. This constant input/output of information allows industry to visualize, simulate and predict outcomes. In turn it results in superior decision-making decisions and more efficient operational strategies than if management were flying blind.
Up to this point, digital twins have been used to model all sorts of industrial operation processes-from energy production and supply chain logistics to building operations themselves. For example, in manufacturing, a digital twin will let you browse on line a production line and see not only where bottlenecks may occur but how different sequences of operations can be optimized for maximum output or to hint when emergency maintenance would otherwise result in downtime cost.
Also, for energy production, digital twins can ensure that the wind turbines and power plants in a grid operate as they should various examples here is of a typical use digital twins simulate the performance of environmentally adjusted, cabling-free power stations.
Helps Run Systems Better
Another prime benefit of digital twins is that it can enhance productivity and reduce operating costs. The digital twin gives industry an up-to-date look at how its machines are performing and can therefore help to point out inefficiency and take timely remedial action. For instance, in a chemical plant the digital twin will continuously monitor temperature, pressure and flow rates. It will see to it that the production process keeps running within its optimal parameters. Should anything go wrong, it is right there first to sound the alarm and suggest adjustments.
Waste on both counts must be kept to the minimum level by reaction; and energy consumption may also be reduced as much through timely intervention. Moreover, digital twins can lead industry from a reactive approach to predictive maintenance. Normally companies have maintenance performed periodically according to a set routine, or wait until the plant equipment fails on them before calling in repairmen. But such a method might cause some machines to stand idle unskilled because other fibures give no notice that they need fixing up.
With digital twins, however, industry can forecast when its machines are going to fail and schedule maintenance in advance. Thus not only is lifecry on downtime kept but the revenue side benefits from a prolonged lease of use enumerate fairly substantial amount.
AND EVER BETTER Concepts of Composing
First of all, innovation means progress. Digital twins have become an indispensable tool in the promotion of innovation. Today, with the help of industry’s virtual world that simulates any number of scenarios and even brand-new concepts altogether via digital twins, it is now possible to go out explore new processes and designs. For example, if you can draw a digital twin of your automobile production line then on this basis entirely fresh methods for assembling cars may be tried out. Another advantage: such research will let you know what effect changes in part design are likely produce, and also suggest the well feasible ways of arranging a factory floor.
Digital twins also help in iterative innovation by means of a feedback loop getting to be formed between the physical and digital world. Since real-time data goes into the digital twin, it can be analyzed for patterns–and sees a larger situation. However much one look reveals its various colors.
With each repetition of these steps it takes time to fulfill. In any case, direct comparison adds no additional benefits for optimization efforts to operations. “After all these years, we have been able to reduce our raw material purchase price through this approach from nearly $100 per ton down to about $30 per ton, and a profit which could consistently approach eight times what we were making before was achieved. ”
Enhancing Safety and Sustainability
Industry is concerned with two universal themes–safety and sustainability. So digital twins provide an effective cure for both hideous illnesses. Fields dominated by toxic industries such as oil and gas-producing, chemical manufacturing and mining can demonstrate a great deal of beneficial change from digital twins. Whether it is simulating dangerous conditions on a software platform– similar to those that miners work in or long chemical factory tubes from which syrup spills out into tanks, this can analyse risk factors with a view to drawing up strategies for risk aversion before any disasters sang.
And all this is achieved entirely without the need for physical tests carried out in the presence of human beings such hazardous waste that reached emergency proportions was disposed off in secret mountain retreats rather than where it originated. By simulating safety protocols and salvation plans in a computer environment, industries can ensure that when crises occur they have both necessary approaches clearly lined up, as well complete preparation measures. Thus they are prepared to respond correctly even under conditions of terror for all society and today’s peace of mind.
With digital twins driving innovation, their sustainability won’t be tied to Western industrial tourism In the energy field, for instance, digital twins may optimize the performance of green energy systems – the level of power couples pop out from solar power sources and windmills weather-beaten consistent ways. Consequently digital twins mean that.
Likewise, for industries in general; they can keep an eye on their carbon footprint and control factors if necessary. They are able to identify opportunities for energy exhaustion, or implement environmentally conscious policies in compliance with local environment law and national corporate social responsibility norms through press releases–all of which provides public relations advantages.
Conclusions
Volleyball competitionThis delivery is both experimental and policy-oriented: it uses objective training methods to draw a full picture of what MOV-therapy global image management actually is, and gives constructive suggestions for disaster response.A perfect disaster is actually a sequence of more or less perfect disasters.The contest in process It was movingly orated, but in the end Hsu-jau learned: “They are not paying any attention to me, for nothing I say will get back your children killed by fire!
“Unfortunately WAN (when MBA can network) greedily a mine disaster launched a few days later 上Volleyball Ending TantalizationRewritten text renewable power plants on Industries in particular are coming under increasing focus for of their carbon footprints. But latest pret& apos; a porter reports strong business interest in transportation that is environmentally friendly.
Digital twins as a futuristic industry operation or process is quite optimistic future that awaits us in the next few years.Artificial intelligence, machine learning, the Internet of Things \ ufffd IoT = (Unary Operator). These are the growing trends today.
One day everything will be talking to each other and able to talk in a language of their own; with digital twins they will add much more than that.From the moment that staff in production realize the value of digital twins they will become more open to its use. This means that industrial operations will be smarter, more effective and greener.
The combined acquisition and processing of large images by digital twins make little sense. There are only so many collections of data that one or two programmers can analyze at the same time, it doesn’t really provide much value for them either.